Every part of industrial machinery is essential to ensuring that it operates smoothly and effectively. The Pilot Bore Sprockets are one such crucial component. This small but mighty piece of equipment, though sometimes disregarded, can significantly impact the functionality and durability of your apparatus. In this article, we’ll discuss what pilot bore sprockets are, how they function, the various types that are on the market, and how to pick the best one for your requirements. So fasten your seatbelt as we explain everything you need to know about these unsung industrial machinery heroes!
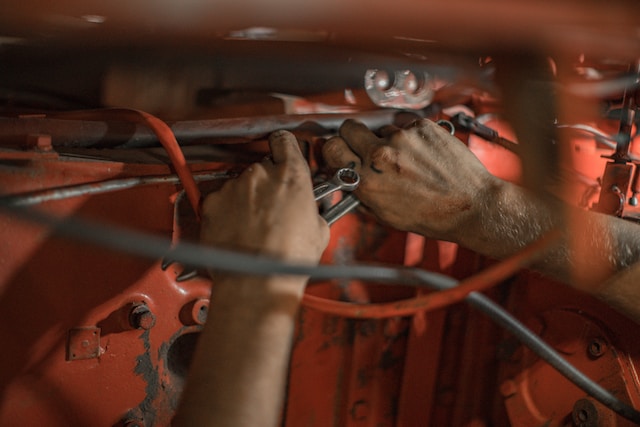
Pilot bore sprockets: what are they?
A particular kind of sprocket used in industrial machinery to transfer rotational power from one shaft to another via a chain is called a pilot bore sprocket. They have an unthreaded bore that makes it simple to install and remove them from the shaft without causing any damage to it.
The phrase “pilot bore” describes how these sprockets don’t actually contain finished holes; instead, they serve as a pilot or guiding surface for drilling and reaming operations by machine shops or end users. With this design, users can alter the bore size to suit their own requirements, making them very adaptable.
Pilot bore sprockets provide a number of benefits, one of which is cost effectiveness because they can be made in large quantities and to standardised standards. Additionally, the fast replacement of this kind of sprocket makes it easier to enhance the performance of your system or replace it when it wears out.
Pilot bore sprockets serve a significant role in maintaining efficient operation and smooth operation, despite their seeming modest size in comparison to other parts of machinery systems.
Pilot bore sprocket advantages
Pilot bore sprockets are a crucial part of industrial machinery that has many advantages. First of all, because they are made to be interchangeable, it is simple to replace damaged or worn-out components without removing the complete apparatus. This reduces downtime while saving time and money.
Pilot bore sprockets’ durability is another benefit. These sprockets can resist big weights and fast revolutions without quickly wearing out since they are made of high-quality materials like steel or cast iron.
Pilot bore sprockets’ precise production method also enables them to run smoothly and effectively with little vibration and noise. Longer-term machine performance becomes more dependable as a result of this.
The advantages of employing pilot bore sprockets show why they are strongly advised for any industrial machinery application where dependability, durability, effectiveness, and versatility are essential elements.
There are various kinds of pilot bore sprockets
Depending on the particular application, different types of pilot bore sprockets can be employed with industrial machines. One kind has a flat hub and bolts directly onto a shaft without the requirement for a keyway. This kind is called a Type A pilot bore sprocket. This facilitates rapid and simple installation.
Another kind is the Type B pilot bore sprocket, which includes a tapered bushing and more mounting possibilities as well as more flexibility in shaft size. Additionally, the bushing contributes to reduced operating noise and vibration.
The Type C pilot bore sprocket is comparable to the Type B, but it also has an extra set screw for extra slippage protection. This particular kind of sprocket is frequently employed in situations where severe weights or shock loads could be present.
Specially made for use with double-strand roller chains are Type D pilot bore sprockets. To handle both strands of chain simultaneously, they have two sets of teeth.
There are specialised pilot bore sprockets available, such as ones with self-lubricating or toughened teeth. These kinds might be required in specific, high-demand settings where wear and tear must be kept to a minimum.
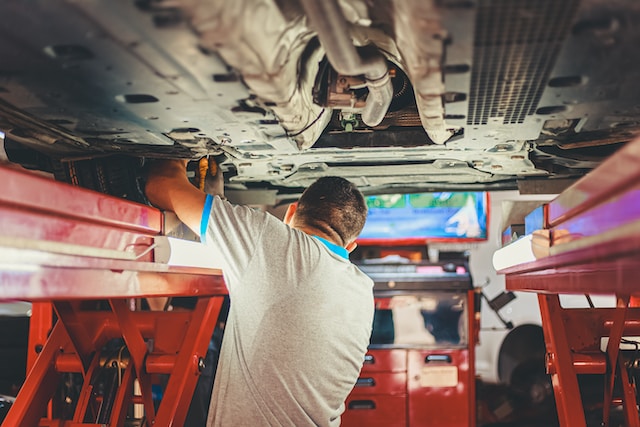
How to select a pilot bore sprocket that will meet your demands?
The proper pilot bore sprocket selection is essential to the efficient running of your industrial gear. Before making a purchase, take into account the following factors:
1. Size
Make sure the sprocket size you select corresponds to the shaft size and chain pitch of your machine.
2. Substance
Take into account the sprocket’s substance because it influences its strength and longevity.
3. Teeth on your sprocket
The amount of teeth on your sprocket will decide how quickly or slowly your machinery runs, so be careful to select the right number of teeth.
4. Load capacity
Determine whether the sprocket can support the weight and pressure load that your machine requires.
5. Maintenance requirements
If you want to save time and money on repairs and replacements, pick a low-maintenance pilot bore sprocket.
Pilot bore sprockets, despite appearing to be minor parts of large-scale machinery, are crucial to the effective operation of those machines. They offer benefits that cannot be exaggerated, including better machinery lifespan and general reliability due to their higher power transfer capabilities and lower shock loads. This makes them crucial components for anyone wishing to maximise the productivity of their equipment.